Disk air diffuser Φ260mm 3m3/h
R320.00 Excl. VAT
Rubber (EPDM) disk diffuser, 250mm diameter, for 3000 liters per hour air.
- Description
- Additional information
- EPDM diffuser disk specification
- Maintenance
Description
This rubber disk diffuser with a 260mm diameter delivers 3000 liters per hour or around 50 liters per minute with a typical head loss equivalent to 20 to 40 cm water column pressure depending on the air flow rate. The lower the air flow rate, the lower pressure loss. Other pressures to take into account when selecting a suitable blower are the water depth and estimated pipe friction losses. PVC fittings not included.
For small systems at 1.5m water depth, a 100 watt LP 100 blower will support two of these diffusers. At the 3m of a water tank, it will support 2 diffusers.
The 850 watt GHBH 2R3 will support around 25 to 30 of the 260mm disc diffusers at 1.5m water depth. The lower the airflow through a diffuser, the lower the energy consumption. Total head loss is increased through the counter-pressure from the membrane that increases with higher airflow, so increasing the compressor/blower power consumption (kWh).
For a good technical document on EPDM diffusers, see Grundvos Technical Specification for aeration.
Rubber poly (EPDM) diffusers: EPDM stands for ethylene propylene diene monomer.
Pipe diameter size selection is important. For instance, when a dimension of ∅110 for the lateral pipe is used, it is possible to use a pipe length of up to 45 metres with 70 diffusers per pipe, while still maintaining practically the same airflow capacity between the first and the last diffuser. The system must be designed so that the air velocity in the air distribution pipes will not exceed 10-15 m/s, as this will create an unacceptable increase in head losses and increase the noise level as well as create a risk of vibrations from the piping.
Additional information
Weight | 1 kg |
---|---|
Dimensions | 30 × 30 × 10 cm |
General parameters for the EPDM diffuser disks
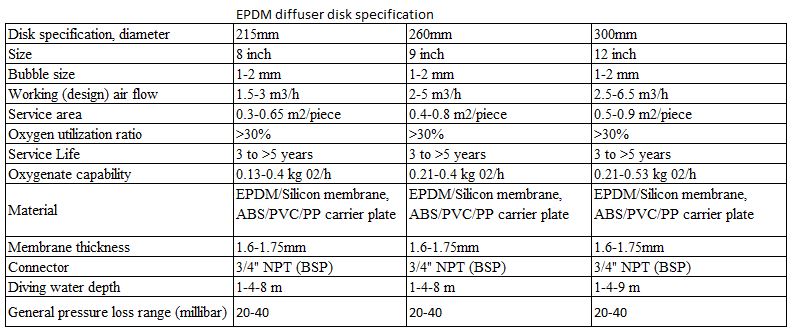
Diffuser maintenance
Organic growth or biofilm may need to be removed should there be a noticeable decrease in air flow.
One successful method is the mechanical cleaning with a high-pressure cleaner. Before the cleaning, the tank has to be drained down to the diffuser level. It is recommended to leave the diffuser elements covered with water (e.g. 0.1 m). The diffusers can remain installed and should be operated with little airflow. A high-pressure water jet is applied several times onto the diffuser surfaces. It is important to work with a dirt blaster rotary nozzle.
Water can accumulate in pipes and will need to be purged. The hot air in the system condenses readily in the submerged aeration grid, with water collecting at the lowest points.
The purge valve may be manual flushing of the line via a valve releasing all the air to the atmosphere. Another tools is an inline purge valve.
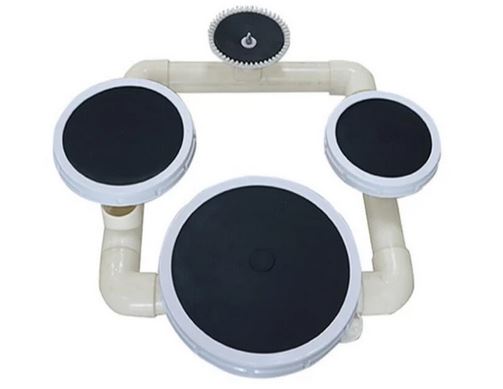
The discharge points of the purge system can be either above water in a manual system (tap), or at the bottom of the basin in a continuous automatic purge system. The manual system is more time-consuming, but is effective and gives visual verification. The water colour will also show if there is a damaged diffuser. Clean water is only condensed water, indicating a system in good condition. A combination of both types of purge system provides additional assurance that the condensed water is being removed at all times and running costs kept to a minimum.
Disc diffusers and pipe diffusers bot have porous membranes. Fundamentally there is no difference between the two types of diffusers and one can easily be chosen over the other for either bottom-mounted or retractable air diffuser systems without compromising aeration needs or system performance. Disc diffuser is easy to install and is not as affected by the turbulent forces in the basin as a tube diffuser is.